
Tensile Canopy University Cricket and Basketball Stadium Patna Bihar

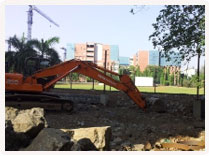
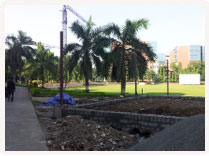
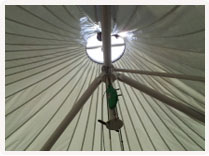

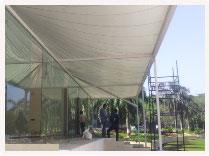
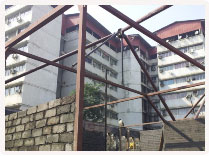
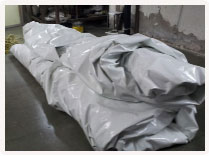

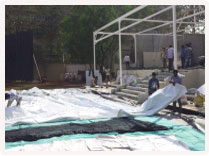
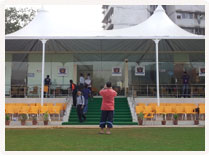
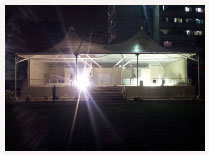

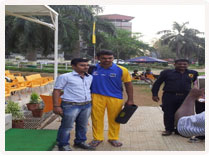
|


Attached to the Football and Cricket stadium, is the University Ground where there is a Tensile Fabric Structure roof, where there are international standards maintained. The Ground is mainly used for various National tournaments, IPL preselecting Matches, and of course for internal college tournaments for 4000 plus students studying within the complex. Usually a makeshift pavilion is created for short term use during the season which is neither comfortable nor durable. With more & more value being given to these games, both economically and socially, especially the IPL, there was an urgent need for a functional pavilion for players of both teams & umpires along with VVIPs.

With the limited time of 30 days, we must design, Analyze, Fabricate, Install a large ( 5000 sq. ft plus ) span Pavilion with a Tensile Membrane structure roof complete with glass facades, Air conditioning, with all Fitness equipments, Rest rooms facilities, etc. peripheral solutions.

The challenge here was to complete the whole project right from basic planning to finishing touches on execution, in less than 30 days, with no design ready, no decision on exact Fabric Form, overall dimensions, & the worst part being that the Area marked for the Pavilion was not leveled, & all the work including the foundation for the structure had to start from scratch.
In short the biggest obstacle faced in execution of this project was that of time, which was allotted to us only at a third of usual time taken.


The Total open Area situated in Patna, Bihar to be covered was marked roughly to be 475 sq. meters


Keeping in mind 30 meters frontage & Highest intermediate columns permitted to be 2, to get the work started even before the foundations are cast, a simple rectangular design form of twin cones, symmetrical about both X & Y axis was suggested. For getting the head start High Engineering standards with a very tight dimensional control were set. The two twin cones to have a common edge were proposed to be convex shape eliminating any chance of pending water in the central area. The Glass facade (12 mm Toughened glass) were suggest all along front & half of the side edges of the pavilion.


Detailed Analysis of the structure was carried out with Internationally acknowledged FEM software,. In absence of Local codes for Governing construction of Tensile membrane structures, EURO standards were followed to generate wind loads depending on geometry, height of structure, height from sea level, dist from sea, surface roughness, topology, etc. The wind pressure for wind speed of 110 km/Hr, followed by various factors to take care of the variable mentioned above was used.
Once structure was analyzed, the dimensional detailing of each individual structural member was carried out after STAAD analysis depending on the max. Load generated in load combinations. Auto cad 2011 was used for Detailing- drafting purposes


The Primary structure supporting the Tensile Fabric membrane was Fabricated out of welded ERW square Pipes (C class) with section, 150 X 150 mm sq. The overall height of the structure was kept at 5 meters above ground level; the peripheral members were also fabricated from the same sections. The Radial members supporting central junction box with arrangements to lift the bail Ring supporting the fabric at centre were fabricated from Die 165 mm X 6 mm Round pipes. Stiffener pipes in the corner ensured tensional rigidity of structure under wind conditions.
The top ring Die 800 mm supported on Die 140 mm Mast which in turn was supported by 3 radial members, 2 from each of the outer corners & 1 from the central wall Partition ( for Umpires cabin ) embedding Vertical columns. With the length of the Radials over 12 meters with only 3 supports (usually 4 diagonal) ensured a wide UN obstructed front view with very few hindering direct view of the fabric.


For the site located in Patna, Bihar the Ferrari 902 S, PVC coated fabric was patterned radically in all 30 / 36 patterns, depending on the size of the cone. To absorb higher stresses towards the Ring center the fabric was reinforced with another layer of 902S membrane patterned in floral shape.
The fabric was fixed on the Top edge of the square Beams with the help of clamping stainless steel strips of 40 mm X 8 mm, separated by Neoprene rubber Gaskets, with help of Self threading extra large screws. The fabric was clamped to the central Bail Ring with help of Stainless steel Nut bolts.


The steel Fabrication was completed within 12 days at the site. All the members once ready coated with 2 coats of epoxy primer, were assembled with the help of hydraulic crane in about 2 days. The overall dimensional tolerance of 5 mm & symmetry was maintained. The painting of the ready structure was started immediately.
Due to symmetry we were able to start working on the patterns almost simultaneously. By the time the painting was completed the Fabric was ready duly welded dispatched to site.
The other civil work like flooring, Italian marble, rest rooms, in all 8, painting of the outer walls etc took another 8 days delaying the fabric installation by almost a week. Thanks to smart Project Management team we still had 4 days to spare for the fabric installation.
As the crane cannot have access to the pavilion from the ground or left or right side, the whole Fabric lifting was carried out manually. The mammoth task of lifting the 5000 sq. ft plus fabric was carried out by our installation team of 10 craftsmen. In about 16 hrs we could lift the fabric to top of the bail ring with help of various tools & Fixtures designed to hold / lift & spread the fabric without soiling it. The floor of the Pavilion was still being finished. The fabric never touched the floor.


Complete pavilion ready in 30 days flat- that too in a perfectly pristine condition...NOTHING SHORT OF A BIG ACHIEVEMENT!!!
